Facilities, Expertise, and Advanced Product Technology
The RENO Team has a long history of supplying iron foundries with high-quality refractory products, ladles, tear-out and reline services, and pre-cast specialty items. Foundries that take advantage of our scientifically advanced products enjoy higher profits through increased production, scrap reductions, energy savings, or ergonomic benefits, versus the standard purchasing goals for reduced item costs. We are pleased to raise the standard for our offerings with our newest and most advanced refractory technology, RENO ElectroCast™, and our Mastermelt DE-OX Product Line.
Cupola Furnaces
RENO has set the standards for long running cupola campaigns. These furnaces melt high ratios of steel and iron scrap along with digesting many contaminants. Each zone requires special attention. For example, a ductile pipe plant will require combustion and a melt zone refractory much different than furnaces melting automotive castings.
RENO is recognized as the industry leader for cupola refractory technology. We employ our US Patented Shot-Crete RENO Jet Cast™, and our US Patented No-Cement Gunning Method, RENO NC Gun™, for the majority of the refractory linings used in the high production cupola furnaces throughout North America.
Well
Wall & Floor Safety: 4.5” Arch Brick (walls) Straights (floors) x 70% Low Iron Brick
Hot Face: RENO ElectroCast™ 1116 SiC and RENO NC SIC
Maintenance: RENO NC Gun 6044 and RENO Gun BTW
Combustion & Melt Zones: Well to 10′ above tuyeres
Ductile Iron Pipe: RENO Cast 9010 CRM, cast and dried or precast design. Ductile pipe plant hottest temperatures, and exposure to high amounts of ferrous oxides in the slag, similar to a steel melting furnace.
Automotive: RENO Jet Cast NC ATZ or RENO NC 90 SiC, both utilize the sol-gel colloidal silica + fused alumina/silicon carbide or all silicon carbide mineral compositions for high temperature and normal iron oxide resistance.
Maintenance
RENO NC Gun 90– Ductile Pipe
RENO NC Gun 85 SiC – Automotive Castings
Pre-Heat and Charge Zone
RENO ElectroCast™ 3SB, cast and dried, or precast design. Many cupolas use bauxite containing products, 85% brick, etc. Over time the high iron contents contained in bauxite will allow carbon monoxide to exfoliate the grains and the refractory becomes weak. RENO ElectroCast™ 3SB resists carbon monoxide destruction and provides the abrasion resistance for longer campaigns.
Combustion Chambers
RENO Jet Cast Super Abrade 60 RENO was the first company to provide shotcrete. This is our proven low cement, alkali resistant product for extreme thermal cycling conditions. RENO Lite Gun 40 insulates the steel shell and helps reduce the damage from the numerous cycles and thermal shock, as the insulation allows the hot face refractory to cool at a slower pace than it does without insulation, and it is very easy to install.
Orifice Rings
Precast designs made from Reno Cast 70 KH Hi-Wire Technology
Cupola Furnace applications
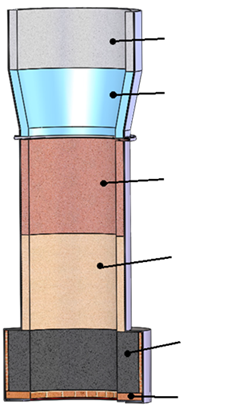
Cross Over Ducts
RENO NC Gun FS
This application must be tight and stable. Our fused silica based refractory can tolerate the temperature swings easily and remains slice in service due to extremely low pore size openings.
Cupola Bottom
The cupola bottom requires refractory products that match the length of the campaign. RENO Bottom Sand is used for short campaigns as a bottom door covering insulation. RENO Cupola Bottom Ram is installed over the RENO Bottom Sand, for a refractory cap. For some plants, they extend the campaign to six months, in these circumstances, RENO Rock BTW Ram is installed over the top of the RENO Cupola Bottom Ram; no Bottom Sand is used for these long campaigns due to the thermal expansion and contraction characteristics of silica.
Tap Hole
Block made with RENO ElectroPump™ 1122 Sic or RENO Rock BTW 2.0 Ram
RENO Rock BTW Plastic rammed around to seal the block
Many cupolas start up with an open tap-hole. This super-hot blast air can oxidize the carbon containing surfaces of castables or resin bonded plastics, and shorten the tap-hole’s useful life. RENO’s new ElectroCast™ Technology seals the porosity with almost zero permeability withstands the molten iron/slag mixtures as well as or better than the traditional products, such as our resin bonded RENO Rock BTW 2.0 Plastic, etc.
Front Slagging Trough
RENO NC 90 SiC castable as the safety lining next to the steel shell. RENO ElectroCast™ 1116 SiC, RENO ElectroPump™ 1122 SiC & RENO Rock BTW 2.0 Ram as the hot face lining.
The front trough hot face must experience and resist 100% of the molten iron and slag produced in the cupola. The most extreme wear is experienced at the cut-line, the metal/slag mixture as this is the most corrosive portion of the layered bath. Velocity and temperatures can affect the wear rates, as well as the metals / alloys / limestone mixtures charged into the cupola. While we cannot control the operational factors, we can offer general rules that can impact the refractory performances; these are: Shape, Safety Lining Selection, and Hot Face Refractory Selection.
Shape
The trough’s hot-face surface can benefit from slowing the velocity of the slag swirling against the slag dam, and circulating back and out of the side cut exit channel. It is imperative to keep the slag chute free and open which reduces the total quantity of slag carried in the trough. Another action that can be done is to reduce the sidewall thickness at the top of the trough to form a V-Shape. This will provide a wider pool which will reduce the height of the slag bath. By using the refractory products selected, this can be safely done in steps, until the pool is enlarged as much as possible. The wider opening also helps when patching as it gives more space if ramming a plastic patch, etc.
Safety Lining 33% of Thickness
Our safety lining, RENO NC 90 SiC, is a 90% containing silicon carbide, no-cement castable. This product is key as it has the highest thermal conductivity to rapidly transfer the heat away from the hot-face. Faster heat sinks, will slow the corrosion at the surface and extend wear rates.
Hot Face Refractory 67% Thickness
The hot face must exhibit high hot strengths to resist the metal and slag rubbing against the sides, as well as the temperatures of the corrosive mixtures. At the cut line, you will see a concave line as if the bath is eating away in a “C-Shape.” Many factors are at play such as miniature explosions of lighting created by the electrical static electricity generated by the passing iron on the grounded refractory. These miniature storms are pushing gases into the refractory structure – this is why the cut line extends above the metal / slag line. These hot dirty gases are the reason; they are being forced into the surface when these electrical charges take place. The only effective way to combat this is to seal the permeability of the refractory structure and prevent these gases from penetrating the structure. RENO’s new scientific breakthrough in refractory bonding technology, RENO ElectroCast™, has produced products unknown to science before now, with almost zero permeability, and extremely high hot strengths. These new characteristics provide the longest lasting refractory for cupola trough campaigns.
Vertical Channel Furnaces
Refractory performance is critical for these furnaces, holding or melting iron. The following products have extended the performance life due to their ability to withstand thermal cycling, slag removal and increased production rates. Coupled with our Mastermelt DE-OX, energy savings, due to free flowing inductor loops, carbon and silicon losses are eliminated and reduced slag volumes are setting new operational standards.
Inductor
RENO ElectroVibe 943 M
Electro-bonding imparts reduced dusting and elevated density. Our alumina-magnesia-spinel, dry vibratable refractory displays non-wetting and resistance to inductor loop buildup behavior.
Throat & Floor
RENO ElectroVibe 92
While cleaning, the oxygen lance can damage silicon carbide bearing refractory below metal line. This product contains all pure alumina + a mullite bonding system.
Insulation and Safety
Floor: ½” Marinite Board, + 3” of 70% Brick
Throats: ¼” Microtherm Overstitch Panels, folded under the brick work
Channel Holding Furnace applications

Walls
Insulation and Safety: RENO Coat It AL on Steel Walls, prevents carbon transfer
4.5” Super Duty Brick, arch type for tight construction
1.5” BNZ 2600°F IFB for Insulation
RENO MO Super 3 Mortar
Hot Face: RENO ElectroCast™ 1110 SiC
New insulation design reduces energy consumption while providing a true safety liner. The freeze plane is well in front of the brick safety lining.
Roof
Insulation and Anchors: 85% Phos Anchor Brick, and ½ Inch Marinite Board
Hot Face: RENO NC 60 with 3% HCA Fibers
Spouts
Hot Face: RENO ElectroCast™ 1110 SiC
Surface Treatment: RENO ElectroCoat™ 75 SiC
Mastermelt Additive
Ductile Iron Base: Mastermelt DE-OX D-1
Gray Iron Base: Mastermelt De-OX
These additives are used to eliminate the oxygen molecules contained in the molten iron. These oxygen molecules are extremely hyper-reactive, and combine in a fraction of time to form spinel formations such as calcium oxide, magnesium oxide, and other tramp element combinations. Since the loop is circulating the metal and the water-cooled bushings create a strong thermal gradient to keep the refractory from melting away, these spinel formations readily stick to the inside of the inductor loops, and form crusts. These crusts reduce the interior cross sectional areas and thus reduce the amounts of electrical current used for conduction and the melting rates slow, while energy consumption soars. Many plants incorporate a cleaning method known as super heating. This is an uncontrolled event and is used to melt away the interior crusts. While it is expensive, it is also dangerous for the refractory compositions making up the loop channels. With Mastermelt DE-OX for GRAY IRON, and Mastermelt DE-OX D-1 for DUCTILE BASED IRON, (Low Sulfur) provides the foundry melt managers with a tool to clean away the buildups and restore the conductance ratios back to nominal states. This new technique is made possible by the science of the Mastermelt TECHNOLOGY.
Another benefit is the change in the slag consistency as the glassy sticky mess is converted to dry lumps that is easily removed.
Coreless Induction Melting Furnaces
Furnaces can now be lined with our RENO Electro MulVibe 60. This new mullite product can tolerate the temperature swings with the pressure from charging and discharging and variances in electric power forces. The high turbulence washes away the surface glass formed with silica/boron compounds and leads to short life. Reno has designed a new concept for combatting the wear mechanisms with our new RENO Electro MulVibe 60 and RENO ElectroSil™ 0.8. The benefits include longer campaigns which reduce refractory consumption, reduce hazardous silica exposure to the personnel, and additional production time.
Cover
Insulation and Anchors: #310 SS VS-Anchors and 1/2″ HD Board
Hot Face: RENO NC 60 with 3% HCA Fibers
Surface Treatment: RENO ElectroCoat™ 75 SiC
Walls and Floor
Reno’s proprietary pure silica refractory utilizes smaller crystals that can tolerate rapid heating and cooling for longer performance life, especially true with the medium frequency furnaces.
RENO Electro MulVibe 60 and RENO ElectroSil™ 0.8 for the Floor and Lower Walls
RENO Sil 1.0 and RENO ElectroSil™ 0.8 for the Upper Walls and Top Cap
Spouts
Hot Face Precast made from Reno ElectroCast™ 370 with 3% HCA Fibers
Surface treatment RENO ElectroCoat™ 75 SiC
Lower Rings
Reno Cast 95 LCT The higher alumina tabular product will transfer the heat faster from the lower walls and floor, and provide additional lining life to the most troublesome areas.
Top Cap Maintenance
If the top cap area is worn, a combination of RENO MO 80 PT can be used to form a bond between a rammed repair using RENO Plastic 85 P, or use our no cement castable, RENO FireCast 70.
Coreless Induction Melting FCE applications
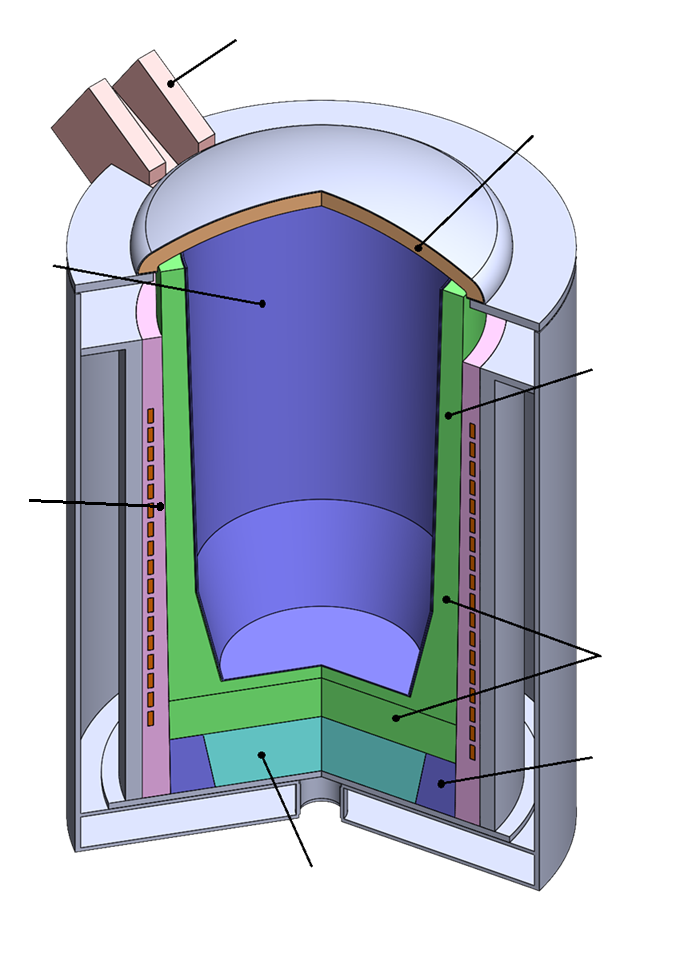
Ductile Treatment Ladle
Reno Refractories, Inc. is proud to introduce our new refractory technology, “Reno FireCast SiC” and “Reno FireCast 70”. These are working blue collar type no cement water based technologies which provide the lower porosity and amorphous bonds in place of the crystalline bonds inherent in cement bonded refractory. Ductile treatment ladles will perform longer and provide labor and alloy savings as well as lower turnaround maintenance costs for our valued customers.
Hot Face / Surface Treatment
RENO Mag Seal and RENO Mag Patch 92
Magnesia Fade is a common problem throughout the ductile iron making industry. If one examines the slag adherences, the compositions are mainly magnesia + calcium + silica; the alloys used for nucleating the carbon flakes into spheres for ductile iron. The magnesia is attracted to silica, which is inherent in most refractory products. RENO has developed a strong air-setting magnesia surface treatment that inhibits the magnesia transfer. Rather than the magnesia lightweight air-setting products, that have little strength, our RENO Mag Seal is robust and strong to resist violent reactions during inoculation treatments. RENO Mag Patch 92 is designed more like a putty texture and is beat for use in the reaction chamber.
Castable Lining
RENO FireCast SiC BF and RENO FireCast 70
A major technology first is RENO’s water based non-cement technology castables which deliver the combined features of low porosity, thermal cycle resistance and lower costs when compared to our sol-gel or electro-bond product line. These products are user friendly in every aspect of use: east to cast, easy to dry and require no additional liquids. Combining the magnesia working surface and the castable back up will provide much longer campaigns before removing for cleaning.
Safety Interior Steel Surface Treatment
RENO Coat It AL, Prevents Carbon Transfer
Benefits
Reduced alloy costs, reduced cleaning labor, decreases safety and workers’ compensation claims, increased production and higher quality as the interior remains a stable size for accurate alloy additions, insulation, and safety liner.
Treatment Ladle applications
Insulation
2800° F, IFB Brick Split / RENO MO Super 3 Mortar
Top Compression Cap
Install a rolled heavy 3-4″ angle iron with gussets for tri-axial compression
Porous Plug, De-Sulphurization Ladles — “Bubbling Pots”
RENO Refractories, Inc. is proud of our world-leading no-cement nano-bonded colloidal silica products.
RENO NC Nano-Tech Technology
All of our NC products provide properties that are unmatched, by any other refractory supplier; these are:
- Low permeability
- Resists penetrations
- Very high hot strengths
- Impact resistance
- Pore sizes are 2-3 microns
- Molten slags do not wet the structure
- Abrasion values below 6 cc loss
- Lasts longer with high turbulence
Bubbling Pot applications
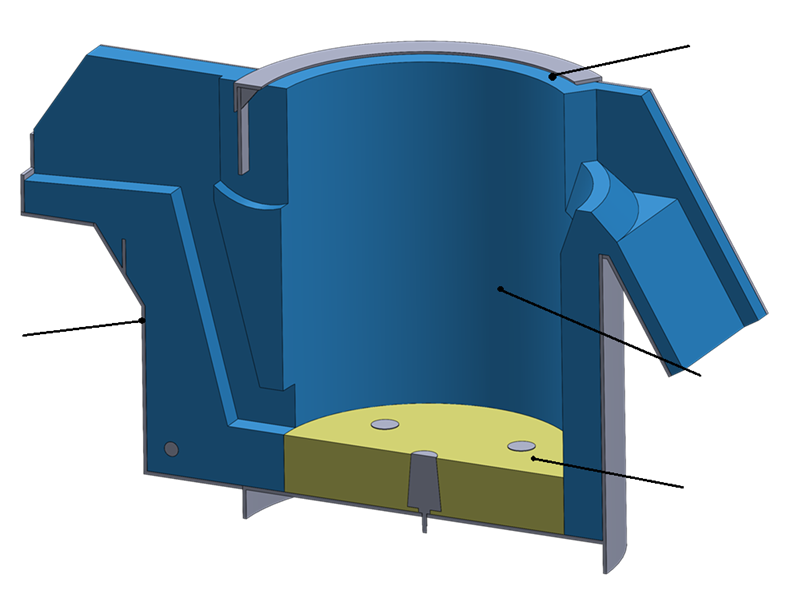
Hot Face/Surface Treatment
RENO ElectroCoat™ 75 SiC
RENO has taken the new Electro technology and produced a near zero permeable structure surface treatment that contains high levels of Silicon Carbide.
Castable Lining
RENO NC 6059 Coarse
RENO uses the strength of an all bauxite product with silicon carbide to further increase thermal shock resistance and reduce surface corrosions from the high levels of lime and spar fluxes.
Floor
RENO NC 60
This no cement castable will last longer and is easier to remove than the coarse grained wall lining when replacing the porous plugs.
Safety Steel Surface Treatment
RENO Coat It AL, Prevents Carbon Transfer
Insulation
2800°F IFB Brick Split / RENO MO Super 3 Mortar
Top Cap
Install a rolled heavy 3-4″ angle iron with gussets for tri-axial compression which eliminates cracks and increases ladle life.
Ductile Iron Pressure Pour Furnace
Inductor Case
RENO ElectroVibe 943 M is a high purity fused alumina based refractory with spinel forming additions. Special Additives are used to aid the densification process. High density and a homogeneous microstructure can be obtained with vibration tools.
Throat & Floor
RENO NC 908
While cleaning, the oxygen lance can damage silicon carbide bearing refractory below metal line. This alumina chrome no cement castable is easy to dry out and provides nanoparticles which reduce pore size and permeability.
RENO ElectroVibe 92
A high purity fused alumina based refractory which provides a very dense and low porosity lining. This new electro technology includes special additives which aid in the product’s compaction.
Pressure Pour Furnace applications

Insulation & Safety
Floor: ½” Marinite Board, + 3” of 70% Brick
Throat: ¼” Microtherm Overstitch Panels, folded under the brick work
Roof
Insulation and Anchors: 85% Phos Anchor Brick, and ½” Marinite Board
Hot Face: RENO NC 60 with 3% HCA Fibers
Spouts
Hot Face: RENO ElectroCast™ 1110 SiC
Surface Treatment: RENO ElectroCoat™ SP
Walls
Insulation and Safety:
RENO Coat It AL on Steel Walls, prevents carbon transfer
4.5” Super Duty Brick, arch type for tight construction
1.5″ BNZ 2600°F IFB for insulation
RENO MO Super 3 Mortar
Hot Face:
RENO ElectroCast™ 1110 SiC
Fused alumina based castable with silicon carbide additive developed with a our proprietary electro chemical bond system for maximum performance.
Grey Iron Auto Pour Furnace
Inductor Case
RENO ElectroVibe 943 M is a high purity fused alumina based refractory with spinel forming additions. Special Additives are used to aid the densification process. High density and a homogeneous microstructure can be obtained with vibration tools.
Throat & Floor
RENO ElectroCast 3SB
While cleaning, the oxygen lance can damage silicon carbide bearing refractory below metal line. This product contains zero carbon, for safer conditions and very high densities and extremely low permeability for clean surfaces when in contact with grey iron.
RENO ElectroVibe 92
A high purity fused alumina based refractory which provides a very dense and low porosity lining. This new electro technology includes special additives which aid in the product’s compaction.
Auto Pour Furnace applications

Insulation & Safety
Floor: ½” Marinite Board, + 3” of 70% Brick
Throat: ¼” Microtherm Overstitch Panels, folded under the brick work
Roof
Insulation and Anchors: 85% Phos Anchor Brick, and ½” Marinite Board
Hot Face: RENO NC 60 with 3% HCA Fibers
Spouts
Hot Face: RENO ElectroCast™ 1110 SiC
Surface Treatment: RENO ElectroCoat™ SP
Walls
Insulation and Safety:
RENO Coat It AL on Steel Walls, prevents carbon transfer
4.5” Super Duty Brick, arch type for tight construction
1.5″ BNZ 2600°F IFB for insulation
RENO MO Super 3 Mortar
Hot Face:
RENO ElectroCast™ 1110 SiC
Fused alumina based castable with silicon carbide additive developed with a our proprietary electro chemical bond system for maximum performance.
Gray Iron Transfer Ladles
RENO FireCast 70 and RENO ElectroCoat™ 75 SiC
Grey Iron Transfer Ladles will perform longer and provide lower turnaround maintenance costs when utilizing these advanced refractory products.
Hot Face/Surface Treatment
RENO ElectroCoat™ 75 SiC is employed to provide a near zero permeable structure surface treatment that contains high levels of silicon carbide. Ladles are much easier to clean. RENO BlakIce 2, is a low cost carbon wash which helps the ladle cleaning from splash and normal use.
Castable Lining
RENO FireCast 70
A major technology first is Reno’s water based non-cement technology castables which deliver the combined features of low porosity, thermal cycle resistance and lower costs when compared to our sol-gel or electro-bond product line. These products are user friendly in every aspect of use: east to cast, easy to dry, and require no additional liquids.
RENO Cast 65 XCLC
Our standard ultra-low cement castable is engineered to tolerate thermal cycling and displays very good abrasion resistance for impact areas.
Insulation
2800°F, IFB Brick Split / RENO MO Super 3 Mortar
Gray Iron Transfer Ladles applications
Safety Surface Treatment
RENO Coat It AL
To prevent Carbon Transfer should molten iron touch the steel shell, which weakens the steel and is the major cause of run-outs, apply this ceramic layer of protection.
Top Cap
Install a rolled heavy 3-4″ angle iron with gussets for tri-axial compression which eliminates cracks and increases ladle life.
Pouring Boxes, with Stopper Rods
RENO NC 6059 Coarse, RENO ElectroCoat™ 75 SiC, RENO NC 908
Pouring Boxes are a constant source of maintenance, as the indexing molds require even and consistent filling via a nozzle and stopper rod assembly. RENO provides the longest casting solutions with our novel pre-cast Nozzles which dispenses the metal in a constant clean flow rates that do not require the continuous stoppage of the molding lines in order to clean, “ROD-OUT” the nozzles. RENO’s innovative designs allow the interior surfaces to run cleaner and longer for reduced change out sequences, which provides more castings and lower costs.
Pouring Box applications
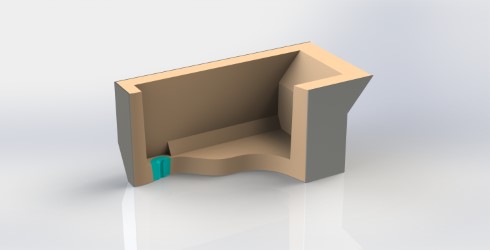
Hot Face/Surface Treatment
RENO ElectroCoat™ 75 SiC is a robust, near zero permeability, ceramic coating that resists oxidation. This new surface will: extend the on-line performance time without buildups, greatly lessen the cleaning time, and allows the castable working lining to last many times longer.
Castable Lining
RENO NC 6059 Coarse
This rugged refractory castable is engineered to tolerate extreme thermal cycling, very small pore sizes, which reduce adherences, and easy dry-out characteristics.
Precast Nozzles
RENO leads the industry with clean metal dispensing, with pour-box nozzles fabricated with RENO NC 908. This is our calcium free product that is virtually pure alumina and chrome oxide enhanced for clean and dependable mold filling. At the end of the day, the extra molds filled, adds profits for the foundry operation.
Insulation
2800°F, IFB Brick Split / RENO MO Super 3 Mortar
Safety Steel Surface Treatment
RENO Coat It AL
To prevent carbon transfer should molten iron touch the steel shell, which weakens the steel and is the major cause of run-outs, apply this ceramic layer of protection.
Top Cap
It is imperative to keep the castable working lining in compression to avoid horizontal cracking; this can be accomplished by incorporating:
3/8” diameter x # 304 V-Anchors welded on 6-inch centers x a length of approximately 80% of the total lining thickness
4 ~ 6-Inch top-cap of RENO Cast 70 KH, HI WIRE
This economical solution can be cast along with castable but the high volume of steel fibers adds a robust, in the field thrust plate barrier to keep the ladle in compression which eliminates cracks and increases life.
Side Charge Cupola and Trough applications
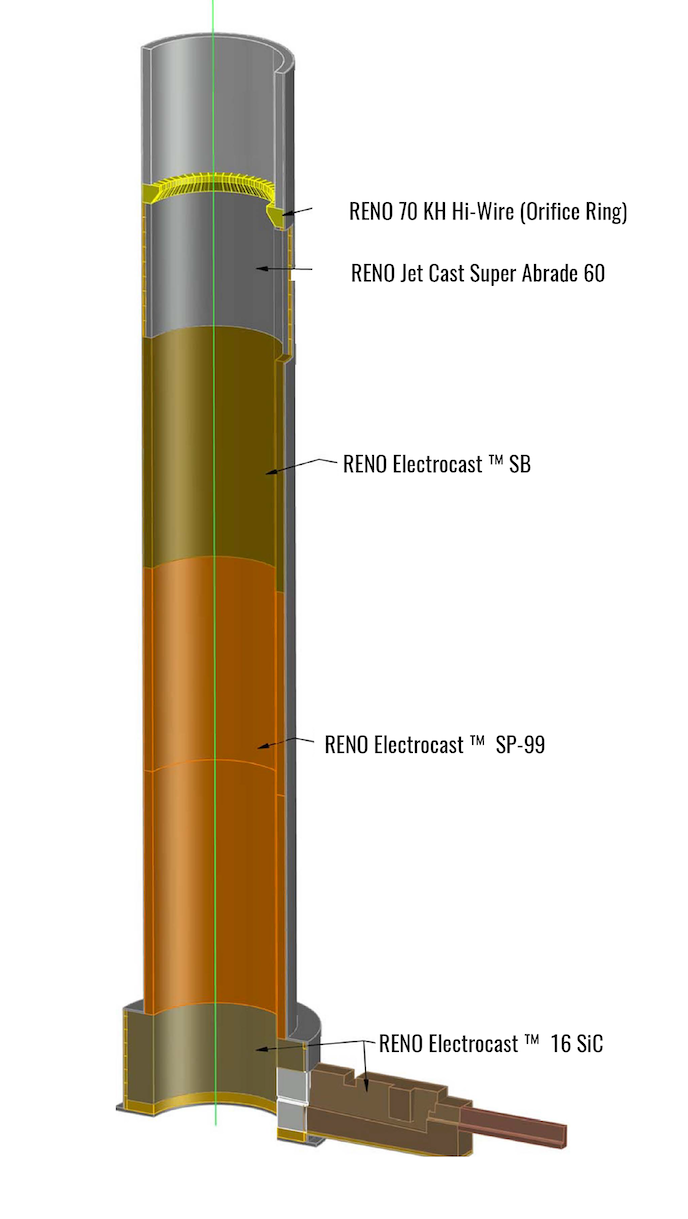
Cupola — 360° Gas Offtake w/ Trough applications
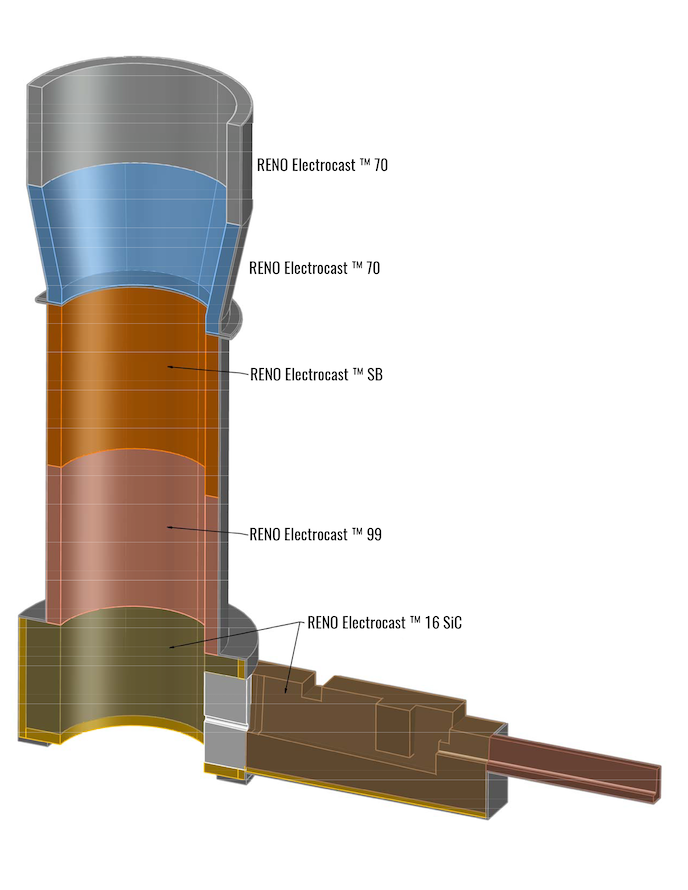
Cupola Furnaces
RENO has set the standards for long running cupola campaigns. These furnaces melt high ratios of steel and iron scrap along with digesting many contaminants. Each zone requires special attention. For example, a ductile pipe plant will require combustion and a melt zone refractory much different than furnaces melting automotive castings.
RENO is recognized as the industry leader for cupola refractory technology. We employ our US Patented Shot-Crete “RENO Jet Cast™,” and our US Patented No Cement Gunning Method, “RENO NC Gun™”, for the majority of the refractory linings used in the high production cupola furnaces throughout North America.
Well (Wall & Floor Safety/Hot Face/Maintenance)
4.5” Arch Brick (walls) Straights (floors) x 70% Low Iron Brick
RENO ElectroCast™ 316 SiC
RENO NC Gun 6044
Combustion & Melt Zones (Ductile Pipe Plant)
RENO ElectroCast™ SP 392, Cast and Dried or Pre-Cast Design, Hottest temperatures, and exposure to High amounts of Ferrous Oxides in the slag, similar to a steel melting furnace
Maintenance
RENO NC Gun 90, RENO Gun SP 92, Ductile Pipe
RENO NC Gun 6044 HT, Automotive Castings
RENO NC GUN 85 SIC, Iron and steel
Pre-Heat and Charge Zone
RENO ElectroCast™ 3SB, cast and dried or (Pre-Cast Design Preferred) Many Cupolas use bauxite containing products, 85% Brick, etc. Over time the high iron contents contained in bauxite will allow carbon monoxide to exfoliate the grains and the refractory is destroyed from the inside of the structure.
RENO ElectroShot™ 1170 if the installation method dictates a shot-crete installation.
Combustion Chambers
RENO Jet Cast Super Abrade 60 RENO was the first company to provide shot-crete, this is our premium low cement, alkali resistant product for extreme thermal cycling conditions.
RENO Lite Gun 40 insulates the steel shell and helps reduce the damage from the numerous cycles and thermal shock, as the insulation allows the hot-face refractory to cool at a slower pace than it does without insulation, and it is very easy to install.
Orifice Rings
Precast designs made from Reno Cast 70 KH Hi-Wire Technology
Cross Over Ducts
RENO ElectroShot™ SIL 1199
This application must be tight and stable, our new All Silica based refractory can tolerate the temperature swings easily and remain slick in service due to the extremely low pore size openings.
Tap Hole
Pre-Cast Block made with RENO ElectroCast™ SP 392
RENO ElectroCoat™ Vapor Shield is used as a surface treatment inside the tap-hole cavity
RENO Rock BTW Plastic rammed around to seal the block
Many cupolas start up with an open tap-hole. This super-hot blast air can oxidize the carbon containing surfaces of castables or resin bonded plastics, and shorten the tap-hole’s useful life. RENO’s new ElectroCoat™ Vapor Shield Technology seals the porosity with almost zero permeability which shields the carbon inside the refractory from the hot blast air at start up. This small step can provide much longer performance time.
Front Slagging Trough
RENO NC 90 SiC castable as the safety lining next to the steel shell
RENO ElectroCast™ 316 SiC as the hot face working lining
The front trough hot face must experience and resist 100% of the molten iron and slag produced in the cupola. The most extreme wear is experienced at the cut-line, the metal/slag mixture is the most corrosive portion of the layered bath. Velocity and temperatures can affect the wear rates, as well as the metals, alloys, and limestone mixtures charged into the cupola. While we cannot control the operational factors, we can offer general rules that can impact the refractory’s performance; these are: Shape, Safety Lining Selection, and Hot Face Refractory Selection.
Shape
The troughs hot-face surface can benefit from slowing the velocity of the slag swirling against the slag dam, and circulating back and out of the side cut exit channel. It is imperative to keep the slag chute free and open, which reduces the total quantity of slag carried in the trough. Another action that can be done is to reduce the sidewall thickness at the top of the trough to form a V-Shape. This will provide a wider pool which will reduce the height of the slag bath. By using the refractory products selected, this can be safely done in steps, until the pool is enlarged as much as possible. The wider opening also helps when patching as it gives more space if ramming a plastic patch, etc.
Safety Lining 33% of Thickness
Our safety lining, RENO NC 90 SiC, is a 90% containing silicon carbide, no-cement castable. This product is key as it has the highest thermal conductivity to rapidly transfer the heat away from the hot-face. Faster heat sinks, will slow the corrosion at the surface and extend wear rates.
Hot Face Refractory 67% Thickness
The hot face must exhibit high hot strengths to resist the metal and slag rubbing against the sides, as well as the temperatures of the corrosive mixtures. At the cut line, you will see a concave line, as if the bath is eating away in a “C-Shape.” Many factors are at play, such as miniature explosions of lighting created by the electrical static electricity generated by the passing iron on the grounded refractory. These miniature storms are pushing gases into the refractory structure – this is why the cut line extends above the metal / slag line. These hot dirty gases are the reason; they are being forced into the surface when these electrical charges take place. The only effective way to combat this is to seal the permeability of the refractory structure and prevent these gases from penetrating the structure. RENO’s new scientific breakthrough in refractory bonding technology, RENO ElectroCast™, has produced products unknown to science before now, with almost zero permeability, and extremely high hot strengths, these new characteristics provide the longest lasting refractory for cupola trough campaigns.
New Advanced Technologies:
RENO ElectroCast™ Technology
- Almost Zero Permeability
- No Alkali or Iron Oxide Penetrations
- Super High Hot Strengths
- Impact Resistance
- Pore Sizes below 1-micron
- Molten Slags do not Wet the Structure
- Abrasion Values below 3 CC Loss
- Lasts Longer with High Volume Charging
- Lower Modulus of Elasticity
- Resists Thermal Cycling Damage
Mastermelt DE-OX
When Mastermelt DE-OX is injected through the tuyeres, iron oxide inside the cupola is eliminated. The oxidizing waste for carbon and silicon losses disappear. Temperature, chemistry and production controls are now achievable with a much more efficient furnace. The overwhelming savings are realized with coke and silicon savings.
Channel Holding Furnace applications
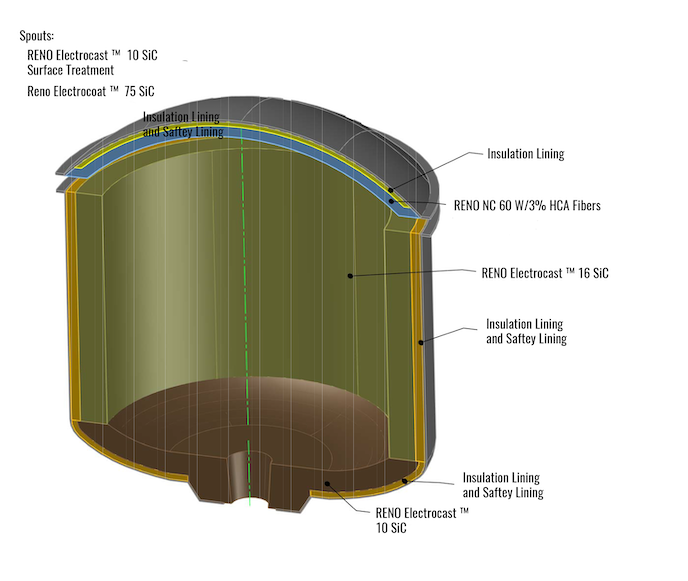
- RENO Electrocast™ 310 SiC
- Surface Treatment: RENO ElectroCoat™ 75 SiC
- Insulation Lining
- RENO NC 60 w/ 3% HCA Fibers
- RENO Electrocast™ 316 SiC
- RENO ElectroCast™ SP 392
Channel Induction Furnaces
Refractory performance is critical for these furnaces, holding or melting iron. The following products have extended the performance life due to their ability to withstand thermal cycling, slag removal, and increased production rates. Coupled with our Mastermelt DE-OX, these products will create massive energy savings, due to free flowing inductor loops, carbon and silicon losses that are eliminated, and reduced slag volumes that are setting new operational standards.
Throat & Floor
RENO ElectroCast™ SP 392
While cleaning, the oxygen lance can damage silicon carbide bearing refractory below metal line. This product contains zero carbon, for safer conditions.
Insulation and Safety
Floor: ½” Marinite Board, + 3” of 70% Brick
Throats: ¼” Microtherm Overstitch Panels, folded under the brick work
Walls
Insulation and Safety: RENO Coat It AL on Steel Walls, prevents carbon transfer
4.5” Super Duty Brick, arch type for tight construction; 1.5 inches of BNZ 2600°F IFB for Insulation RENO MO Super 3 Mortar. New Insulation-design, reduces energy consumption while providing a true safety liner. The freeze plane is well in front of the brick safety lining.
Hot Face: RENO ElectroCast™ 316 SiC, and RENO ElectroCast™ 310 SiC
RENO’s new advanced electro-bonded technology is used for designing the hot-face refractory compositions with super low permeability, and extremely high hot strengths. The attributes contribute to the long-lasting performance and clean interior walls which increases iron melting efficiencies, and reduces electrical power consumption. “Savings for electricity and increased production easily make the refractory cost of no consequence; thus, we provide free refractories when thinking of the cost to savings benefits.”
Roof
Insulation and Anchors: 85% Phos Anchor Brick, and ½ Inch Marinite Board
Hot Face: RENO NC 60 with 3% HCA Fibers
Spouts
Hot Face: RENO ElectroCast™ 310 SiC
Surface Treatment: RENO ElectroCoat™ 75 SiC
Mastermelt Additive
Ductile Iron Base: Mastermelt DE-OX D-1
Gray Iron Base: Mastermelt De-OX
These additives are used to eliminate the oxygen molecules contained in the molten iron. These oxygen molecules are extremely hyper-reactive, and combine in a fraction of time to form spinel formations such as calcium oxide, magnesium oxide, and other tramp element combinations. Since the loop is circulating the metal and the water-cooled bushings create a strong thermal gradient to keep the refractory from melting away, these spinel formations readily stick to the inside of the inductor loops, and form crusts. These crusts reduce the interior cross sectional areas and thus reduce the amounts of electrical current used for conduction and the melting rates slow, while energy consumption soars. Many plants incorporate a cleaning method known as super heating. This is an uncontrolled event and is used to melt away the interior crusts. While it is expensive, it is also dangerous for the refractory compositions making up the loop channels. With Mastermelt DE-OX for GRAY IRON, and Mastermelt DE-OX D-1 for DUCTILE BASED IRON, (Low Sulfur) provides the foundry melt managers with a tool to clean away the buildups and restore the conductance ratios back to nominal states. This new technique is made possible by the science of the Mastermelt TECHNOLOGY.
Another benefit is the change in the slag consistency as the glassy sticky mess is converted to dry lumps that is easily removed.
Coreless Induction Melting FCE applications
- RENO Electrocast™ 370 w/ 3% HCA Fibers
- Surface Treatment: RENO Electrocoat™ SP
- RENO NC 60 w/ 3% HCA Fibers
- Surface Treatment: RENO Electrocoat™ 75 SiC
- RENO SiL 1.0
- RENO SiL 0.8
- RENO SiL 0.6
- RENO Cast 95 LCT
RENO Sil 0.6 and RENO Sil 1.0
RENO’s proprietary Pure Silica Refractory is not made from the traditional low cost quartz found in most competitors’ products. Our product is made from Silica Rock with much smaller crystals that can tolerate rapid heating and cooling for longer performance life, this is especially true with the higher powered, medium frequency furnaces producing ductile based iron.
New RENO ElectroCast™ Technology
These new products provide properties that are unmatched by any other refractory supplier; such as:
- Almost Zero Permeability
- No Alkali or Iron Oxide Penetrations
- Super High Hot Strengths
- Impact Resistance
- Pore Sizes below 1-micron
- Molten Slags do not Wet the Structure
- Abrasion Values below 3 CC Loss
- Lasts Longer with High Volume Charging
Elephant Foot Wear Zone
Precast impact bowl, made with Reno ElectroCast™ Sp 392. This zone experiences temperature swings with the pressure from charging, discharging and variances in electric power forces. The high turbulence washes away the surface glass formed with silica / boron compounds and leads to shorter life. RENO has designed a new concept for combatting the wear mechanisms with our new RENO ElectroCast™ SP 392 product, and our Reno Sil 0.6 as the safety lining. The benefits are much longer campaigns, which reduce hazardous silica exposures for the personnel. Also, less frequent relines offer more production time.
Cover (Insulation and Anchors/Hot Face/Surface Treatment)
85% Phos. Anchor Brick, and ½ Inch Marinite Board
RENO NC 60 with 3% HCA Fibers
RENO ElectroCoat 75 SiC
Spouts (Hot Face/Surface Treatment)
Hot Face Precast made from Reno ElectroCast™ 370 with 3% HCA Fibers
Surface treatment RENO ElectroCoat™ SP
Lower Rings
Reno Cast 95 LCT The higher alumina tabular product will transfer the heat faster from the lower walls and floor, and provide additional lining life to the most troublesome areas.
Walls and Floor
RENO’s proprietary Pure Silica Refractory is not made from the traditional low cost quartz found in most competitors’ products. Our product is made from Silica Rock with much smaller crystals that can tolerate rapid heating and cooling for longer performance life, especially true with the higher-powered medium frequency furnaces producing ductile-based iron.
RENO Sil 0.6 for the Floor and Lower Walls
RENO Sil 1.0 for the Upper Walls and Top Cap
Treatment Ladle applications
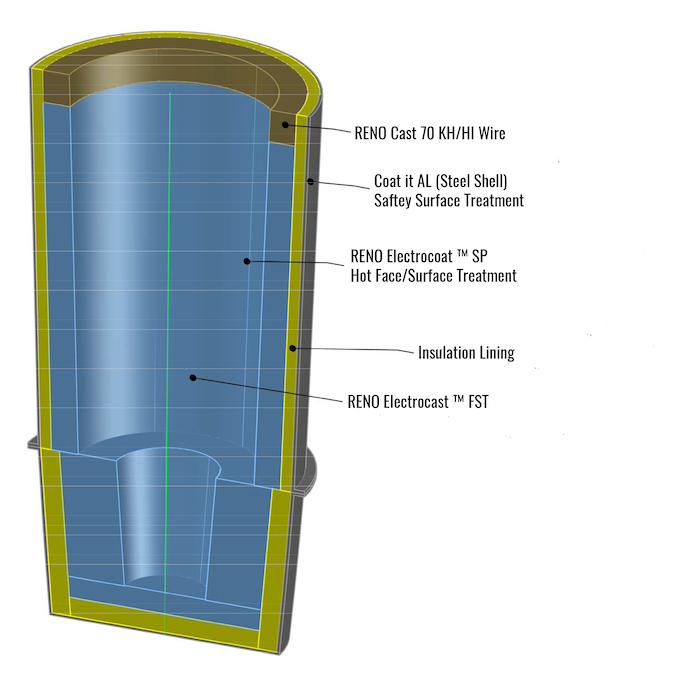
- RENO Cast 70 KH/Hi Wire
- Coat It AL (Steel Shell) Safety Surface Treatment
- RENO Electrocoat™ SP Hot Face/ Surface Treatment
- Insulation Lining
- RENO Electrocast™ FST
Ductile Treatment Ladles
Ductile treating ladles are used for transforming gray iron into nodular or ductile iron. The Magnesia Ferro-Silicon alloys used in this process liberate free magnesia and calcium which rapidly builds on the wall surfaces, requiring heavy cleaning. With RENO’s ElectroCoat™ SP, the castable surface is protected from the magnesia / lime mixtures, and stays clean. This feature allows the ladle to stay in service longer which reduces the cleaning cycles, which saves labor and repair products.
Refractory Surfaces (Hot Face / Surface Treatment)
RENO ElectroCoat™ SP
Magnesia Fade is a common problem throughout the ductile iron making industry. If one examines the slag adherences, the compositions are mainly magnesia + calcium + silica; the alloys used for nucleating the carbon flakes into spheres for ductile. The magnesia is attracted to silica which is inherent in most refractory. RENO has taken the new Electro technology and produced a near zero permeable structure surface treatment that contains zero silica and thus inhibits the magnesia transfer. Rather than the sometimes used magnesia lightweight air-setting products, that have little strength, our RENO ElectroCoat™ SP is robust and strong enough to resist the violent reactions during inoculation treatments.
Castable Lining
RENO ElectroCast™ FST
Another major technology first is RENO’s Synthesized Mineral in combination with our Electro Technology. This product also is silica free and will behave similar to pure mullite in it’s ability to tolerate thermal cycling. Combining the working surface and the castable back up will provide much longer campaigns before removing for cleaning and reduce the very expensive amounts of alloys to provide carbon nucleation.
Safety Surface Treatment
RENO Coat It AL, Pevents Carbon Transfer
Benefits
- Reduced Cleaning Labor
- Increases Safety and Workers’ Compensation Claims
- Increased Production and Higher Quality as the interior remains a stable size for Accurate Additions
Insulation
2800°F, IFB Brick Split / RENO MO Super 3 Mortar
Top Compression Cap
It is imperative to keep the castable working lining in compression to avoid horizontal cracking. This can be accomplished by incorporating:
3/8” diameter x # 304 V-Anchors x length of approximately 80% of thickness, welded on 6-inch centers
4 ~ 6-Inch top-cap of RENO Cast 70 KH /Hi Wire.
This economical solution can be cast along with castable but the high volume of steel fibers adds a robust in the field thrust plate barrier to keep the ladle in compression which eliminates cracks and increases refractory life.
Bubbling Pot applications
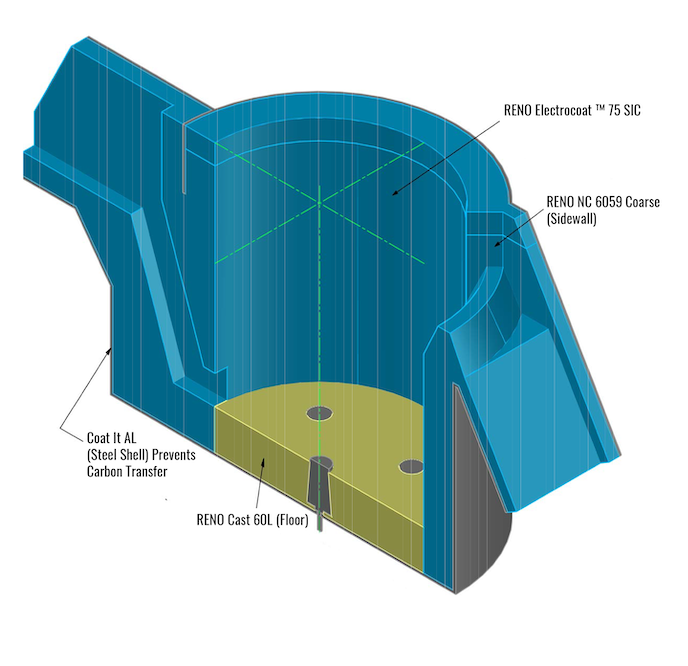
Porous Plug, De-Sulphurization Ladles — “Bubbling Pots”
RENO Refractories, Inc. is proud of our world-leading no-cement, nano-bonded, colloidal silica products.
RENO NC Nano-Tech Technology
All of our NC products provide properties that are unmatched, by any other refractory supplier; these are:
- Low Permeability
- Resists Penetrations
- Super High Hot Strengths
- Impact Resistance
- Pore Sizes are 2-3 Microns
- Molten Slags do not Wet the Structure
- Abrasion Values below 6 CC Loss
- Lasts Longer with High Turbulence
Hot Face/Surface Treatment
RENO ElectroCoat™ 75 SiC
RENO has taken the new Electro technology and produced a near zero permeable structure surface treatment that contains high levels of Silicon Carbide. RENO ElectroCoat™ SP is robust and strong to resist the violent reactions during inoculation treatments.
Castable Lining
RENO NC 6059 Coarse
RENO uses the strength of an all bauxite product with silicon carbide to further increase thermal shock resistance and reduce surface corrosions form the high levels of lime and spar fluxes.
Floor
RENO NC 60
This no cement castable will last longer and is easier to remove than the coarse grained wall lining when replacing the porous plugs.
Safety Steel Surface Treatment
RENO Coat It AL, Prevents Carbon Transfer
Insulation
2800°F IFB Brick Split / RENO MO Super 3 Mortar
Top Cap
It is imperative to keep the castable working lining in compression to avoid horizontal cracking; this can be accomplished by incorporating:
3/8” diameter x # 304 V-Anchors welded every 6-inches apart
4 ~ 6-Inch top-cap of RENO Cast 70 KH HI WIRE
This economical solution adds a robust in the field thrust plate barrier to keep the ladle in compression, which eliminates cracks, and increases refractory life.
Pressure Pour Furnace applications
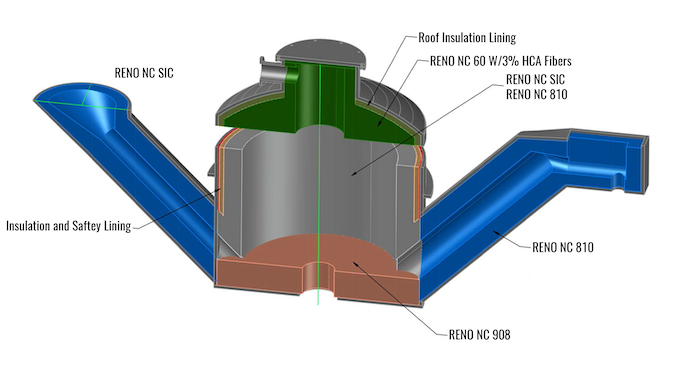
- Roof Insulation Lining
- RENO NC 60 w/3% HCA Fibers
- RENO ElectroCast™ FST
- RENO ElectroCoat™ SP (Surface Treatment)
- RENO ElectroCast SP 392
- RENO Coat IT AL (Steel Shell)
- Insulation and Safety Lining
Ductile Iron Pour Pressure Furnace
Increased Production, and Reduced Cleaning
While in service, the magnesia and calcium carried over from the alloys used in the inoculation process, tends to create a viscous slag layer that can build up on the walls and throat areas. These adherences are very difficult to remove, requiring dangerous hot work to be done on a regular basis. These cleaning activities, reduces valuable production time.
Our super low permeable refractory products, used in many auto-pour and pressure pour furnaces have greatly increased the production time intervals between these cleaning activities, and have lessened the time required to perform the actual cleaning, and increased the refractory life.
Competitive Low Cement Products display a pore size of 20-30 microns.
Our no cement, NC products using the sol gel binder system display pores of 1-2 microns.
RENO ElectroCast™ Products only exhibit pores of 0.5 ~ 0.1 microns!
Throat & Floor
Reno ElectroCast SP 392
While cleaning, the oxygen lance can damage silicon carbide bearing refractory below metal line. This product contains zero carbon, for safer conditions
Insulation & Safety
Floor: ½” Marinite Board, + 3” of 70% Brick
Throats: ¼” Microtherm Overstitch Panels, folded under the brick work
Roof
Insulation and Anchors: 85% Phos Anchor Brick, and ½ Inch Marinite Board
Hot Face: RENO NC 60 with 3% HCA Fibers
Spouts
Hot Face: RENO ElectroCast™ FST
Surface Treatment: RENO ElectroCoat™ SP
Walls
Insulation and Safety:
RENO Coat It AL on Steel Walls, prevents carbon transfer
4.5” Super Duty Brick, arch type for tight construction
1.5 inches of BNZ 2600° F IFB for Insulation
RENO MO Super 3 Mortar
Hot Face:
RENO ElectroCast™ FST
RENO has invested in a new synthetic mineral made exclusively for us. This mineral can tolerate thermal swings, and is non wetting while in contact with iron. Zero Silica composition prevents magnesium fade from ductile iron. Cleaning is made easy and less frequent. New insulation design reduces energy consumption while providing a true safety liner. The freeze plane is well in front of the brick safety lining.
Pouring Box applications
Pouring Boxes, with Stopper Rods
RENO NC 6059 Coarse, RENO ElectroCoat™ 75 SiC, RENO NC 908
Pouring Boxes are a constant source of maintenance, as the indexing molds require even and consistent filling via a nozzle and stopper rod assembly. RENO provides the longest casting solutions with our novel pre-cast Nozzles which dispenses the metal in a constant clean flow rates that do not require the continuous stoppage of the molding lines in order to clean, “ROD-OUT” the nozzles. RENO’s innovative designs allow the interior surfaces to run cleaner and longer for reduced change out sequences, which provides more castings and lower costs.
Hot Face/Surface Treatment
RRENO ElectroCoat™ 75 SiC is a robust, near zero permeability, ceramic coating that resists oxidation. This new surface will: extend the on-line performance time without buildups, greatly lessen the cleaning time, and allows the castable working lining to last many times longer.
Castable Lining
RENO NC 6059 Coarse
This rugged refractory castable is engineered to tolerate extreme thermal cycling, very small pore sizes, which reduce adherences, and easy dry-out characteristics.
Precast Nozzles
RENO leads the industry with clean metal dispensing, with pour-box nozzles fabricated with RENO NC 908. This is our calcium free product that is virtually pure alumina and chrome oxide enhanced for clean and dependable mold filling. At the end of the day, the extra molds filled, adds profits for the foundry operation.
Insulation
2800°F, IFB Brick Split / RENO MO Super 3 Mortar
Safety Steel Surface Treatment
RENO Coat It AL
To prevent Carbon Transfer should molten iron touch the steel shell, which weakens the steel and is the major cause of run-outs, apply this ceramic layer of protection.
Top Cap
It is imperative to keep the castable working lining in compression to avoid horizontal cracking; this can be accomplished by incorporating:
3/8” diameter x # 304 V-Anchors welded on 6-inch centers x a length of approximately 80% of the total lining thickness
4 ~ 6-Inch top-cap of RENO Cast 70 KH HI WIRE
This economical solution can be cast along with castable but the high volume of steel fibers adds a robust, in the field thrust plate barrier to keep the ladle in compression which eliminates cracks and increases life.
Gray Iron Transfer Ladle applications
Gray Iron Transfer Ladles
RENO ElectroCast™ 370 and RENO ElectroCoat™ 75 SiC
Grey Iron Transfer Ladles will perform longer and provide lower turnaround maintenance costs when utilizing these advanced refractory products.
Hot Face/Surface Treatment
RENO ElectroCoat™ 75 SiC is a robust, near zero permeability, ceramic coating that resists oxidation. This new surface will: extend the on-line performance time without buildups, greatly lessen the cleaning time, and allows the castable working lining to last many times longer.
Castable Lining
RENO ElectroCast™ 370
This super refractory is engineered to tolerate thermal cycling and has all the advantages listed for our Electro Castables, such as extremely small pore sizes, and very low permeability, to resist adherences, and very high hot strengths, to combat erosion.
Insulation
2800°F, IFB Brick Split / RENO MO Super 3 Mortar
Safety Surface Treatment
RENO Coat It AL
To prevent Carbon Transfer should molten iron touch the steel shell, which weakens the steel and is the major cause of run-outs, apply this ceramic layer of protection.
Top Cap
It is imperative to keep the castable working lining in compression to avoid horizontal cracking; this can be accomplished by incorporating:
3/8” diameter x # 304 V-Anchors welded on 6-inch centers x a length of approximately 80% of the total lining thickness
4 ~ 6-Inch top-cap of RENO Cast 70 KH HI WIRE
This economical solution can be cast along with castable but the high volume of steel fibers adds a robust, in the field thrust plate barrier to keep the ladle in compression which eliminates cracks and increases life.